
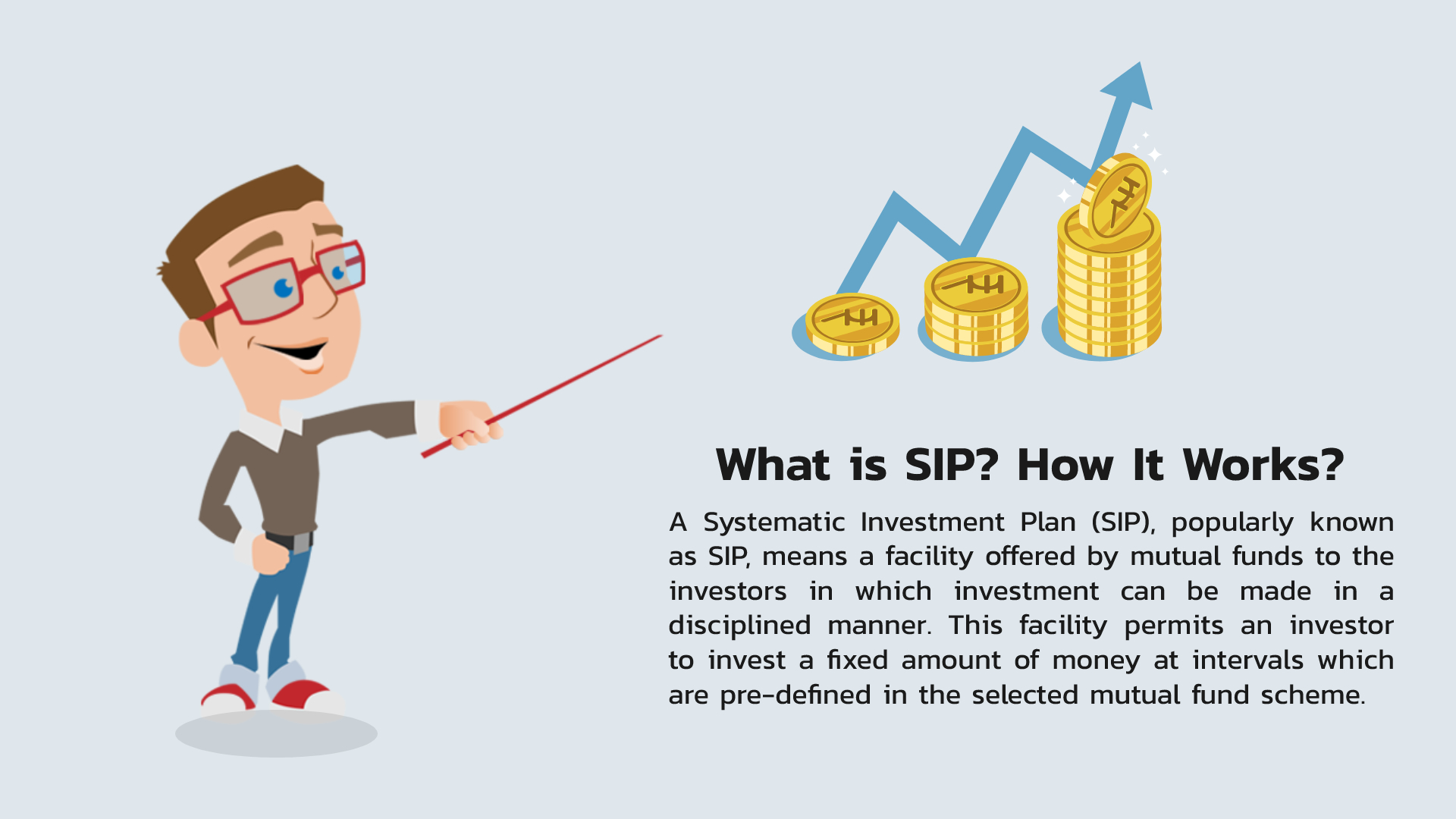
Vertical cuts in the OSB for electrical wiring don’t interfere with the SIP wall integrity however, horizontal cuts significantly reduce panel strength. A specific problem with installing electrical wiring through a SIP wall involves the cutting of the wall. When installing electrical wire through SIPs, builders must hire subcontractors familiar with SIP construction. Horizontal Cutting of the SIPs Diminishes Structural Performance When done correctly, the process provides quality control and minimizes waste however, any mistakes either in design or cutting of the SIPs can cost a builder both time and money. To prevent costly mistakes during SIP installation, architects and builders must plan for the electric wiring and plumbing, the doors and windows, and other architectural features. SIP manufacturers use computer-controlled equipment to size and cut the SIPs according to the CAD drawings. Manufacturers, architects, and builders must ensure precise and accurate cutting of SIPs to prevent time-consuming and costly modifications during installation. Costly Modifications of SIPs During Installation Eleven Problems with Structural Insulated Panels 1. However, the numerous problems with SIP construction can diminish the quality of the wall system and ultimately cost both the contractor and building owner time and money. SIP construction produces straight walls with higher levels of insulation, airtightness, and strength compared to wood-frame construction. Other sheathing materials include plywood, gypsum sheathing, sheet metal, fiber-cement siding, magnesium-oxide board, fiberglass mat, and composite structural siding panels. Producers of SIPs commonly use 7⁄16-inch thick oriented strand boards (OSB) for the sheathing boards.

Manufacturers inject and cure (under high pressure) the liquid PUR and PIR foam.Manufacturer's pressure laminates the EPS and XPS foam and sheathing together.Products used to make the foam include either expanded polystyrene (EPS), extruded polystyrene (XPS), polyurethane (PUR) or polyisocyanurate (PIR). Four- and eight‑inch thick rigid foam panels, placed between two stiff sheathing materials form the SIPs. Manufacturing of SIPs occurs under controlled conditions in a factory. Other names for SIPs include foam-core panels, structural foam panels, stress-skin panels, and sandwich panels. Structural insulated panels provide building panels for the walls, floors, and roofs of homes and light commercial buildings. However, over time, architects and contractors began recognizing problems with SIPs - of concern, SIPs lack moisture−, fire −, and termite-resistance, along with design flexibility.
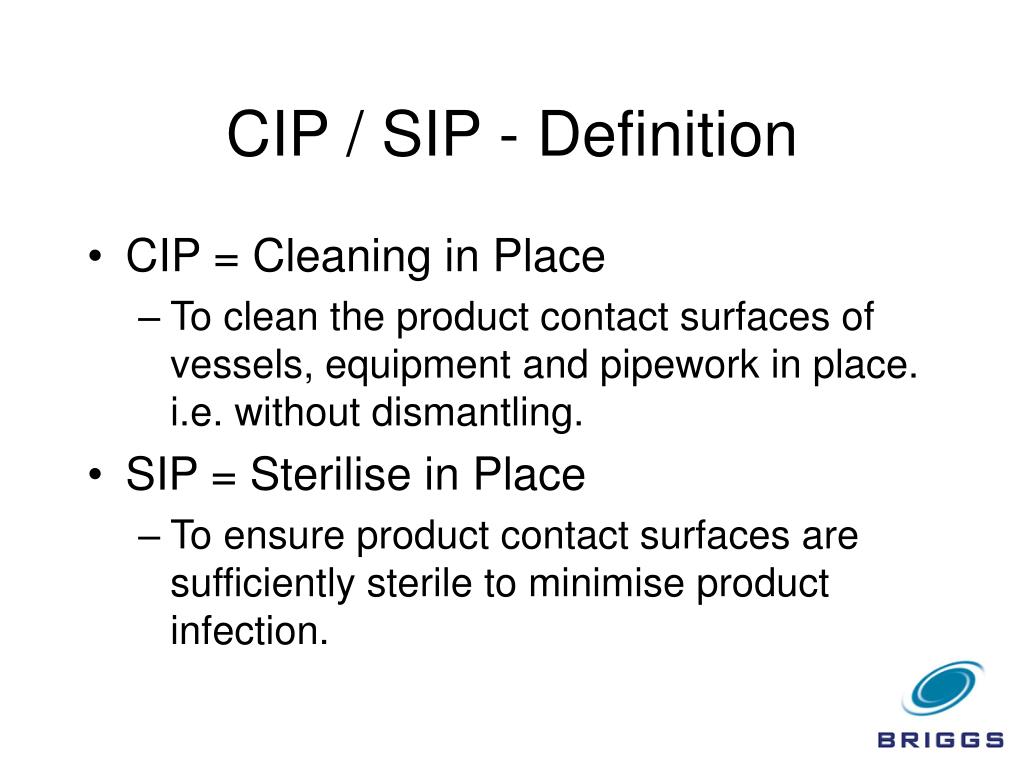
Many credit Dow with creating the first structural insulated panel.ĭuring the 1970s, more and more builders began using SIPs for their high insulative value, airtightness, and strength over wood frame construction. Dow, who was concerned about energy-efficiency and fearful over depleting natural resources, developed a structural panel with an insulated core. However, the design did not contain insulation, and manufacturers never produced it on a large scale. Forest Products Laboratory marketed its initial prototype design for the next thirty years. It was part of the United States (U.S.) Forest Service’s attempt to conserve forest resources. Development of the first SIPs occurred in the 1930s at the Forest Product Laboratory in Madison, Wisconsin.
